Industrial waste organic and inorganic fertilizer spray granulation process
The urea melt granulation process produces waste slag organic and inorganic fertilizers with the following advantages:
The urea slurry directly enters the granulator, which is both a raw material and a liquid phase to participate in the granulation process and provide a certain amount of heat energy; increase the temperature of the material during granulation, reduce the water content of the material, facilitate the formation and drying of the ball; reduce the drying load , reduce coal consumption.
In the NPK ratio, the content of nitrogen nutrients can be increased, and various brands of organic-inorganic compound fertilizers and various trace element compound fertilizers with a total nutrient content of 15% to 35% can be produced.
The output is obviously improved. Because the moisture of the material during granulation is about 3%, the drying capacity of the dryer is greatly improved. Compared with other processes, the yield is increased by 30%~50%, which aims to increase production and reduce costs.
The product quality is obviously improved, the particles are round and smooth, the compressive strength reaches 16N, and the moisture content is low, which solves the problem of agglomeration of fertilizer.
Brief introduction of the process of producing waste organic and inorganic fertilizer by urea melt granulation process:
1) A part of urea is continuously added to the urea melter, and heat is supplied by a steam (heat transfer oil) boiler to melt the urea into a liquid state.
2) After pressurization via a dedicated pump, the urea slurry is atomized and sprayed onto the curtain in the drum granulator.
3) The qualified raw materials such as process waste, urea, monoammonium phosphate, potassium chloride and filler are simultaneously transported to the relevant weighing equipment.
4) The weighed raw material is transferred to the mixer and stirred evenly.
5) transported into the drum granulator, in full contact with the slurry from the melting of the urea melter, while introducing saturated steam, the material forms a rolling bed by the friction generated by the rotation of the drum granulator; The resulting squeezing force and the cohesive force provided by the urea slurry cause the material to stick to the ball.
6) Transfer to the rotary dryer for heat exchange with heat from the hot blast stove.
7) The particles are sorted into the hot sieving, and the fine particles are directly returned to the drum granulator, and as the core, the particles are continuously involved in the cohesion of the particles.
8) The semi-finished particles after screening are transported to a rotary chiller to cool the fertilizer by natural cold air or strong cooling air. The large particles are pulverized by a pulverizer and returned to the drum granulator to continue to participate in the ball formation.
9) The qualified products after screening are transported to the coating machine for coating.
10) Transfer to the fully automatic packaging scale for weighing, packaging and storage.
Drying, cooling and workshop dust are discharged after being treated by cyclone dust collector, labyrinth dust chamber and wet scrubbing.
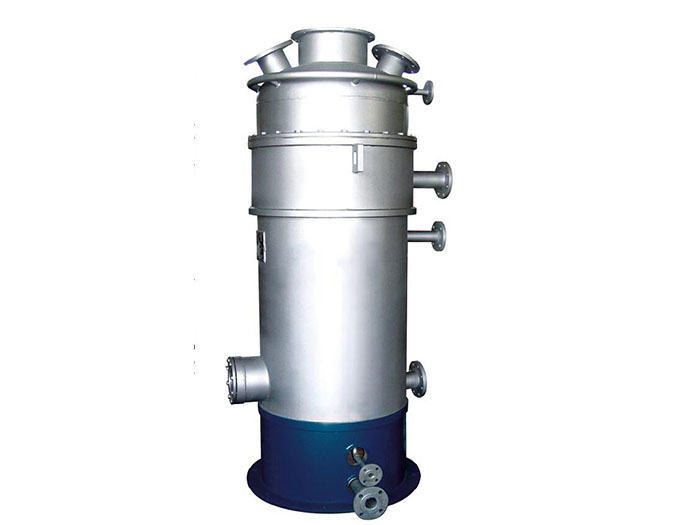
This paper mainly describes the industry, waste organic, inorganic fertilizer, spray granulation, Shandong Huasheng Heavy Industry Co., Ltd.
Industrial waste organic and inorganic fertilizer spray granulation process